数字型旋转圆盘电极装置在材料腐蚀研究中的应用
CO2腐蚀是油气田生产过程中最为常见的一种腐蚀形式,然而在实际油气田管道中,一些因素会导致油气管线内部含有O2形成O2/CO2腐蚀环境。
缓蚀剂作为一种简单有效且价格低廉的抑制CO2腐蚀的措施,被广泛应用于油气田生产过程中。缓蚀剂的作用效果不仅受温度CO2分压,水介质成分的影响,O2对其也有重要影响。目前,O2对缓蚀剂抑制CO2腐蚀的具体影响机制在国内外尚未展开系统的研究。
本工作利用旋转圆盘电极(RDE)腐蚀电化学方法,结合扫描电镜等手段,研究O2对缓蚀剂抑制碳钢CO2腐蚀的影响,从O2影响缓蚀剂分子吸附能力的角度,提出了O2减弱缓蚀剂缓蚀效果的作用机制。
一、实验材料与方法
实验在常压下进行,实验仪器采用数字型旋转圆盘电极装置,测试温度分别为25℃和60℃溶液配好后通CO2气体除氧8h。进行纯CO2条件下实验时,向溶液里持续缓慢通入纯CO2气体,使液保持CO2饱和状态,并防止测试过程中溶解氧进入;进行O2/CO2共存环境下的实验时,向溶液里持续缓慢地通入O2:CO2体积比1:8的混合气体,此时溶解氧含量经溶氧仪测量约1.4×10-6。
实验设计采用电化学“三电极体系”,实验仪器数字型旋转圆盘电极装置主机转速设定为1000r/min,工作电极为有效面积1cm2的圆盘状试样。测试前,用砂纸将试样打磨到2000#,依次用丙酮除油,去离子水冲洗,酒精清洗,冷风吹干。所用辅助电极为铂电极,参比电极为饱和甘汞电极(SCE)。
进行不同缓蚀剂浓度下的缓蚀剂电化学性能测试时,测试温度为25℃,先稳定开路电位30min,然后测试交流阻抗,最后再测极化曲线。交流阻抗测试频率范围100kHZ至10mHz,交流信号幅值为5mV。动电位极化曲线以0.5mV·S-1扫描速率从-0.35V扫至0.35V相对于开路电位。
进行8×10-5缓蚀剂浓度下EIS连续监测实验时,测试温度为60℃,测试开始后,每隔一段时间测试一次EIS,连续测试30h。测试结束后,取出试样,依次用去离子水,酒精清洗,冷风吹干。
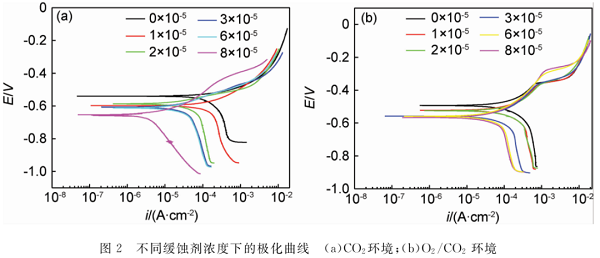
图2(a)为25℃,通CO2气体至饱和,1000r/min转速下,加入不同浓度的缓蚀剂,后所测得的极化曲线。图2(b)为相同条件下通入11.12%氢气后所测极化曲线。
由图2可见,随着缓蚀剂浓度的增加,极化曲线的阴阳极Tafel斜率都发生了改变,而自腐蚀电位负移,可见此种缓蚀剂是以抑制阴极反应为主的混合型缓蚀剂。
利用Tafel曲线外推法,计算出各种条件下的自腐蚀电流密度icorr和缓蚀效率ƞ,结果如表所示。当体系中混入O2以后,在各个缓蚀剂浓度下,自腐蚀电流密度icorr都明显增大,腐蚀速率变大。同时,随着缓蚀剂度的增加,纯CO2环境下,icorr迅速下降,当缓蚀剂浓度到达8×10-5时,缓蚀效率达到了98%以上。而当混入O2以后,最高缓蚀效率只有80%左右。
图2(a)可见,缓蚀剂浓度增加后,阴极Tafel曲线明显变平,缓蚀剂的加入极大地阻滞了阴极过程,从而导致自腐蚀电流密度迅速下降。
对比图2(b)含氧环境下的极化曲线,发现随着缓蚀剂浓度的增加,阴极Tafel斜率并无明显改变,只是整个极化曲线向左平移,因此自腐蚀电流密度icorr减小的程度远不如纯CO2条件下的明显。
对比阳极极化曲线,有氧和无氧条件下都出现了明显的平台区,这是阳极极化电位达到一定程度时,试样表面Fe溶解,导致吸附在上面的缓蚀剂脱附所致。平台区电位即为缓蚀剂脱附电位,当缓蚀剂浓度较低时,脱附电位并无明显差异,当缓蚀剂浓度达到8×10-5时,脱附电位明显变正。
2.2 不同缓蚀剂浓度下阻抗谱分析
图3为纯CO2和O2/CO2环境下所测得的阻抗谱.由图3可知,两种条件下,不含缓蚀剂及含较低浓度缓蚀剂时,阻抗谱由一个容抗弧构成。当缓蚀剂浓度增加时,阻抗谱由双容抗弧组成。在纯CO2环境下,当缓蚀剂达到8×10-5时,低频区还出现了一个小感抗弧,这是缓蚀剂吸附过程所致,而O2/CO2环境下则没有出现。
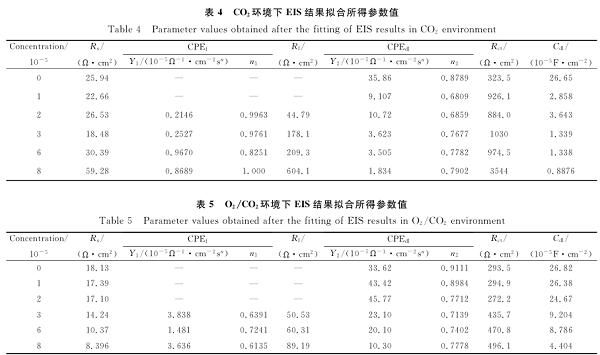
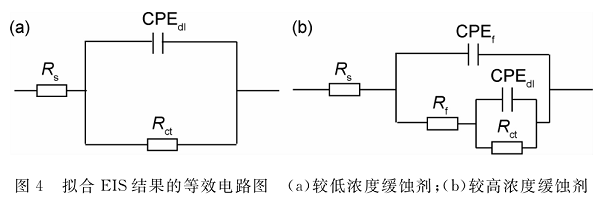
利用阻抗谱拟合软件Zsimpwin进行拟合,所得结果如图4所示。缓蚀剂浓度较低时,利用图4(a)所示的等效电路进行拟合,其中Rs为溶液电阻,CPE为常相位角元件,Rct为电荷转移电阻。高缓蚀剂浓度时,利用图4(b)所示的等效电路进行拟合,其中Rf为试样表面各种物质形成的膜的电阻,Rct为电荷转移电阻。
电荷转移电阻Rct能够反映缓蚀剂吸附膜屏蔽腐蚀介质,阻碍腐蚀反应进行的能力,Rct越大,表示缓蚀效果越好,腐蚀速率越低。由表4可知,在纯CO2环境下,加入缓蚀剂以后,Rct迅速变大,同时,Rct随着缓蚀剂浓度的增加也基本保持变大趋势,到8×10-5时Rct,急剧变大,达到3444Ω·cm2,缓蚀效率达到最高。但是,在O2/CO2共存环境下,由表5知,加入较低浓度的缓蚀剂(1×10-5)和(2×10-5)后,Rct基本保持不变,甚至在2×10-5时还略有减小。这可能是因为,一方面,加入缓蚀剂以后自腐蚀电位变负,试样腐蚀的倾向变大,而另一方面,缓蚀剂的浓度增加导致缓蚀剂吸附量增大,吸附膜覆盖率增加,而在2×10-5时,电位变负占据主导地位,从而导致在2×10-5时Rct反常减小。当加入的缓蚀剂浓度达到3×10-5以上时,Rct开始明显变大,且随着缓蚀剂浓度的增加而变大,但是与CO2环境中同缓蚀剂浓度下的Rct相比,仍然要小得多。
如表4所示,在CO2环境下Cdll随着缓蚀剂浓度的增加而急剧下降。当缓蚀剂浓度达到8×10-5时,Cdll从0时的2.665×10-4 F·cm-2降低到了8.88×10-6 F·cm-2。同时从极化曲线计算的缓蚀效率来看,8×10-5时达到98.33%,说明此时缓蚀剂分子在试样表面吸附量很大,吸附膜覆盖十分完整,缓蚀效果好。
对比O2/CO2环境下,如表5所示,缓蚀剂溶度为0时由于表面无缓蚀剂吸附,所以两种条件下Cdll相近。而当缓蚀剂添加到1×10-5和2×10-5时,由于添加的缓蚀剂浓度比较低,含氧条件下,试样表面所吸附的缓蚀剂分子极少,双电层中的水分子只有极少量被取代,所以Cdll基本保持不变。而当缓蚀剂浓度继续增加时,缓蚀剂分子吸附量增加,取代的水分子越来越多,Cdll开始逐渐降低,直到8×10-5双电层电容降为4.40×10-5F·cm-2但仍远大于纯CO2环境下的Cdll。显然,加入O2以后,试样表面吸附的缓蚀剂分子减少了,吸附膜覆盖度减少,即使在8×10-5条件下,其缓蚀效率也只有80.27%,远低于纯CO2环境下的缓蚀剂作用效果。
三、结论
(1) 缓蚀剂对于碳钢的CO2腐蚀具有良好的缓蚀作用,其缓蚀效率在8×10-5浓度下可以达到98.3%,但是加入O2后会明显降低其缓蚀效率,缓蚀效率在8×10-5浓度下也仅有80.3%。
(2) O2的混入会使缓蚀剂更倾向于缓蚀剂分子与缓蚀剂分子之间的结合,而其吸附在碳钢表面的能力则大幅度减弱,导致无法形成完整的缓蚀剂吸附膜,使得缓蚀剂屏蔽腐蚀介质的作用减弱,缓蚀效果变差。
(3) O2的混入使得碳钢腐蚀速率变大,碳钢表面腐蚀产物膜生成速度变快,导致缓蚀剂的有效作用时间变短,生成的腐蚀产物主要由Fe2O3及FeO(OH)组成,且腐蚀产物膜疏松多孔,无法像纯CO2环境下的产物膜一样对基体起到很好的保护作用,同时会导致明显的点蚀出现。
以上内容由理化(香港)有限公司技术中心整理,有不足之处请指正,转载请注明出处。
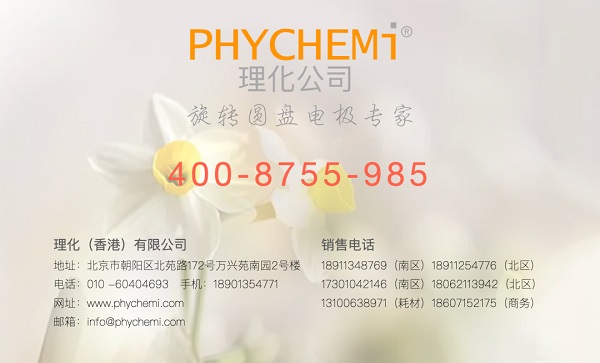